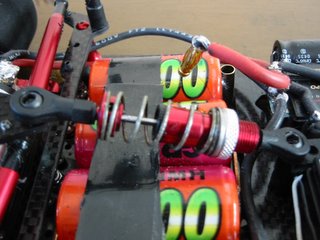
The VCS centre shock and its spring controls the “bend” in the chassis (around the rear pivot point) when power is applied by the motor. Under throttle this spring is going to compress. It will also compress over the bumps.
There is no limit to the compression of this spring other than the chassis bottoming out. I guess you could fit a limit cylinder on the shock shaft but I have never tried this. My gut feel is that the compression evident with the car on the track is a few mm at most.
We do however limit the backward movement of the pod using the length of the VCS shock and its ball joints. The trick is to get the shock length just right according to your required backward movement. This back tilt allows “lift” in the chassis height above the static setting, maximised around the cell area.
I have read recommendations that this allowed “lift” should be around 1mm, however, I have been tuning for no lift at all. I find that the rear end is more predictable this way.
Broken Shocks
The pod back tilt or lift is limited by the shock shaft itself. If you tune for no lift or only 1mm, a crash can cause the chassis to pull the innards of the shock out, which is not good! With the standard Associated VCS shock, the only thing holding the shock together is the plastic “E” clip.
I have started to use the CRC Dura Shock which solves this problem http://www.teamcrc.com/crc/modules.php?name=Shopping_Cart&file=category&category_id=24
I have never had a crash failure with this type of shock.
Improving Shock Balls
Removal of the battery pack can require the removal of one end of the VCS shock. I see people in the pits killing the ball joints with pliers. This cannot be good for the reliability and accuracy in this area.
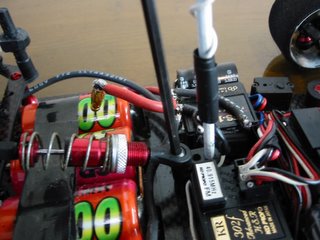
I use the threaded stud type of ball joint used on XRAY touring cars. These are the 303220 and 303240 parts found here:
http://www.teamxray.com/teamxray/products/proddesc.php?prod_id=394&kategoria=1290