Before we can do a fine adjustment on chassis tweak we need to get the basic ride height and rear pod droop set roughly right.
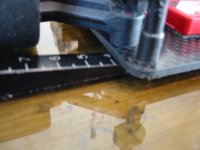
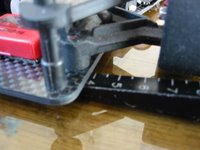
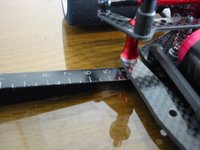
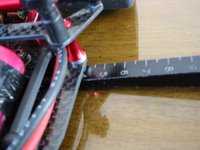
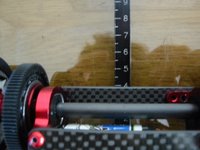
I measure ride height in 5 places as shown in the pictures. These 5 locations tell you a lot about the car. You will need a “wedge” type ride height gauge, not a stepped one. The wedge gauge will allow you to measure ride heights to within 0.2mm. This is the one I own: http://www.hudy.net/xhudy/products/proddesc.php?prod_id=157&kategoria=64
A word about chassis rounding: I notice many people round off the edges of the chassis for a smooth look. Yes ok, this looks nice but you loose the accurate edge against which you can measure ride height…. So I don’t bother.
As you can see in the pictures (4mm ride height intended), I expect to be able to tweak the car out (full instructions later!) and end up with a ride height that is equall from left to right within 01. to 0.2 mm.
Starting Tyre Size
Accurate ride height and setup can only be achieved if you have accurately ground tyres. A good starting point is with 50mm rears and 45mm fronts on the CRC. I like to race nationals with tyres much smaller than this but I start here for club meetings. If you don’t have access to a tyre truer then your ability to set up a 1/12th car is going to be severely limited.
True your tyres and use the rear pod axle spacers and front block shims to get the ride height around 4mm as a starting point. I tend to run ride heights between 3-4mm depending on the quality of the track.
A warning about front block shims.
I use the Fibre Lyte shims http://www.fibre-lyte.co.uk/fl/cars/callandra/calspa.html
The idea is that you can push in the shims in just by loosening the front block screws but there are problems here.
I have found that the “U” shape of the shim allows the block to distort into the open part of the U…. and no, I do not over tighten the screws. This leads to unpredictable geometry at the front.
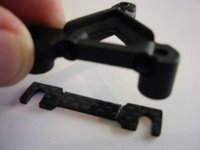
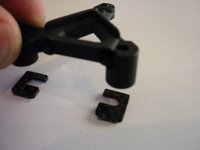
Bad Good
My solution is to cut the shims into four separate “U’s” and turn them through 90 degrees so the block material inboard and outboard of the screw is supported.