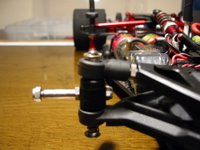
Introduction
I use the Calandra CRC Carpet Knife 3.2R but the following build note apply to any car using the Associated reactive castor "L4" type front end.
I am heading towards explaining how to fully tweak out the CRC Carpet Knife 3.2R chassis. Before we look at the final tuning of the whole car it is important that the Associated front end is built as consistently and accurately as possible.
Get it right!
Fractional errors and “left to right” differences in spring lengths, shimming, block moldings and general alignment within the front end will cause unpredictable handing on the track.
It took me a whole season of 1/12th racing to realise that the driving the car is hard enough on its own without the thing wanting to pull right or left under acceleration. I am not an “inch perfect” driver but I am learning to build and inch perfect car. Unfortunately, predictability measured in inches on the track needs accuracy down to fractions of a millimeter or 1/100th of an inch .. or better!

Step 1 Checking the Lower Arms

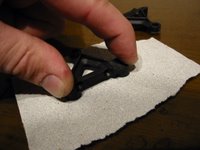
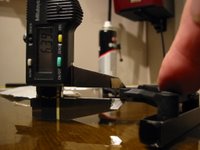
Step 2 Choose your balls
I have found a much better king pin pivot ball than the standard kit part.
The suspension balls I use are Teflon coated. You will end up with a much freer suspension using these parts while keeping the suspension free of play.
http://rc4less.safeshopper.com/22/389.htm?692
I think IRS do these also. Not cheap but worth it… trust me.


Finally, when you push the balls into the moldings, make sure the collar is orientated towards the steering block. The collar will be pointing up in the lower arm and down in the top ball joint.
If you use pliers to force the balls into location, do use some folded paper to prevent the pliers from causing damage.
Step 3 Trim the lower arms
If you use the CRC front axles (as I am sure you do.. the titanium ones are great!) the securing nut on the inside of the front block will hit the lower arm on full lock so some trimming is needed here. The two photos below show this trim.


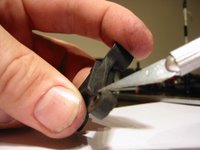
The castor of the steering block (as a result of the king pin angle) tends to make it bind on back edge of the lower arm while steering, lifting it off the lower ball. To stop this, trim some material off of the lower as shown.

Step 4 Polish the king pins

The king pin may be burred where the slot for the E clip has been machined. This makes the king pin slightly oversized and it may scratch the ball as you push it through. A light touch with abrasive paper around the ends followed by a polish will solve this problem.
The king pin moves through the lower arm ball like a piston as the suspension compresses on the spring so it is important to make sure this area runs especially free.
It is also important for the king pin to move freely through the steering block. I use the optional Delrin CRC block. This is more accurate than the stock Associated molding.
http://www.teamcrc.com/crc/modules.php?name=Shopping_Cart&file=product&c_op=viewprod&prodID=7718834
… the reaming for the king pin is really nice and free… but…. There is a problem here. The Delrin blocks include stock axles but if you screw in the CRC threaded axles, the king pin hole tightens up and the suspension will bind.
After screwing in the CRC axles it is necessary to ream out the king pin hole to an accurate 1/8th fitting again. You can do this by hand using a 1/8th drill or (even better) a 1/8th reamer. Alternatively, just stick with the stock axles that come with the blocks.
Step 5 Polish the upper pivot pins
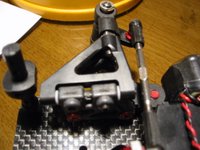
http://www.teamcrc.com/crc/modules.php?name=Shopping_Cart&file=product&c_op=viewprod&prodID=7718833
The upper pivot pin can bind on these arms, mainly because the tolerances in the pivot hole on the CRC part is tighter.


Polish the pivot pins, especially at the ends where the bearing surface is made with the upper arms. You do not need to get the pin to run free in the reactive castor angle block (the 0 degree, 5 degree, 10 degree part), you will probably want to lock the pin in place with a grub screw here anyway to hold the pin fast.
When assembled, the top arm should pivot around the pin with no noticeable friction, damping or binding.
Handling note
I normally run the 10 degree reactive castor block which does offer the most aggressive steering out of the three (10, 5 and 0 degrees). I will reduce to the 5 degree block if the car is too snappy on the front.
Step 6 Shim and Spring the King Pins
Handling note
My starting point is to work with the 0.020 in. front spring. The spring number is referring to the diameter of the wire used to form the coil. The higher the number, the thicker the wire and stiffer the spring. Optional springs are as follows:
0.018 in. Soft
0.020 in. Medium
0.022 in. Hard
0.024 in. very Hard!
Spring Errors


First pick two springs with the same thickness and measure them with your calipers to double check yourself. I know this sounds stupid but I have made mistakes in the past and ended up running different springs left and right!
It is also important that both the springs are the same length to within 0.01 in (0.25 mm) which is the thickness around two shims. If the springs differ by more than this I would assume that one has collapsed and is damaged. Get a new pair.
Adding Shims

The correct shims for this job have an outside diameter of 4.92mm (0.1940 in).
The two shims sizes I have are 0.11 mm (0.0045 in) and double that at 0.22 mm (0.0090 in).
If you use the Teflon coated balls (as mentioned above) with the 0.020 spring and have trimmed the back part of the lower arm also, a good starting point for the shim stack is 2.22mm (0.0870 in). The problem with giving this measurement is that there are so many variables including the balls, steering arm, king pin length and even the E clip thickness.
Step 7 Final Check
Finally mount the front end on the car.
Adjust the servo links for Zero degrees toe. Then use a camber guage to get to set 1 degree of negative camber.

Finally check that the shims have just taken out all of the king pin play and that the suspension has the same free feel when you compare left to right.
Cheers
Mark